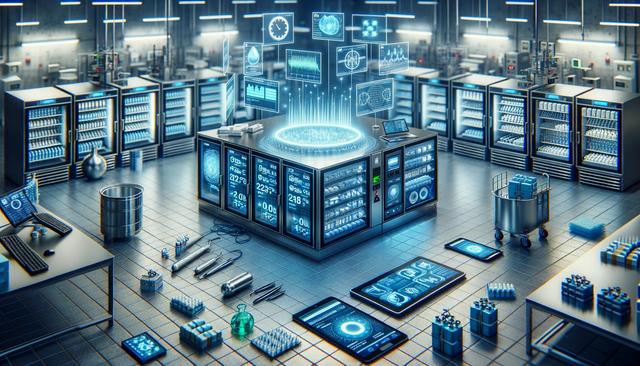
Cold Room Temperature Monitoring System: Essential for Quality Control and Compliance
Why Cold Room Temperature Monitoring Matters
Temperature-sensitive environments are a cornerstone of operations in various sectors, including healthcare, food processing, and pharmaceuticals. Products stored in cold rooms—such as vaccines, perishable foods, and laboratory samples—require constant temperature control to ensure safety and effectiveness. Even slight fluctuations in temperature can compromise product quality or render items unusable. A Cold Room Temperature Monitoring System (CRTMS) plays a vital role in mitigating such risks by providing continuous tracking of temperature levels and alerting operators to any deviations. This real-time monitoring ensures compliance with regulatory standards and supports internal quality control protocols.
Without reliable monitoring, organizations may face significant financial losses due to spoiled inventory, legal implications from non-compliance, and reputational damage. CRTMS solutions are designed to offer timely and accurate data, helping businesses maintain control and accountability over their storage conditions.
Key Features of a CRTMS
Modern CRTMS solutions are equipped with a range of functionalities that enhance their reliability and usability. These systems typically include:
- Digital sensors that provide precise temperature readings
- Real-time alerts via SMS, email, or mobile apps for any deviations
- Data logging capabilities for historical temperature tracking
- Cloud-based dashboards for remote monitoring
- Compliance-ready reporting tools
Some systems also support integration with existing facility management platforms, enabling centralized control. These features not only improve operational efficiency but also reduce the risk of human error, which can occur with manual temperature logs.
The choice of features will often depend on the specific needs of the facility. For example, a pharmaceutical warehouse might prioritize high-accuracy sensors and regulatory-compliant reporting, whereas a commercial kitchen may focus more on immediate alerts and ease of use.
Compliance and Regulatory Considerations
In regulated industries, maintaining proper storage conditions is not just a matter of quality—it is a legal requirement. Agencies such as food safety authorities and health regulatory bodies mandate strict temperature ranges for storing sensitive products. A CRTMS helps organizations meet these requirements by providing:
- Audit-ready digital records
- Automated compliance reporting
- Documentation for inspections and certifications
Failure to comply with these standards can result in fines, product recalls, or even suspension of operations. By using a CRTMS, businesses can demonstrate due diligence and maintain a consistent standard of care in their operations. This is particularly critical in sectors like vaccine storage, where temperature excursions can lead to compromised efficacy.
Integration with Facility Management Systems
Many CRTMS options are designed to work seamlessly with broader facility management systems. This integration allows operators to monitor not only temperature but also humidity, door status, and equipment uptime from a single interface. The benefits of such integration include:
- Consolidated data for easier decision-making
- Improved response times to system alerts
- Enhanced energy efficiency through optimized cooling cycles
For facilities managing multiple cold rooms or geographically dispersed sites, centralized control via a CRTMS offers significant operational advantages. It enables managers to oversee multiple environments without being physically present, which is particularly useful in large-scale distribution or logistics networks.
Moreover, integrated systems can contribute to sustainability efforts by reducing energy waste and extending the lifespan of refrigeration equipment through predictive maintenance alerts.
Choosing and Implementing a CRTMS
Selecting the right CRTMS requires a clear understanding of your operational needs and regulatory obligations. Key factors to consider include:
- Accuracy and reliability of sensors
- Ease of use and scalability
- Compliance features and reporting capabilities
- Support and maintenance services
Implementation should involve a thorough site assessment, proper sensor placement, and staff training to ensure effective use. It’s also advisable to conduct periodic system audits to verify performance and update configurations as needed.
Working with a reputable vendor can aid in customizing the solution to fit specific industry requirements. Whether you are managing a hospital pharmacy or a commercial food warehouse, tailoring the system to your workflow ensures maximum benefit and long-term value.
Conclusion
For industries that rely on temperature-sensitive storage, a Cold Room Temperature Monitoring System is an essential part of quality control and regulatory compliance. By offering continuous monitoring, automated alerts, and detailed reporting, CRTMS solutions help organizations maintain product integrity, meet legal standards, and operate more efficiently. Investing in a robust monitoring system is not just a technological upgrade—it’s a strategic decision that supports operational excellence and long-term sustainability.