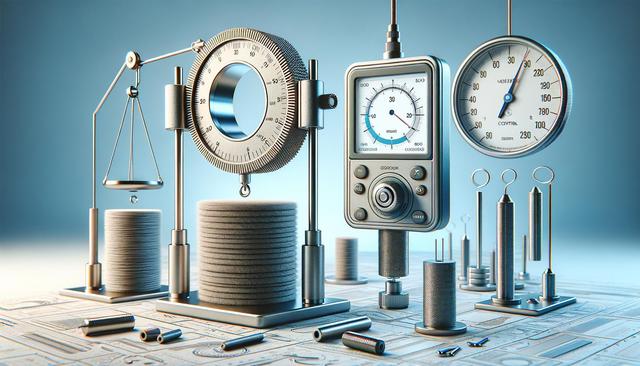
How Extensometers Improve Material Testing and Quality Control
Understanding the Role of Extensometers in Material Testing
Extensometers play a central role in evaluating how materials behave under mechanical stress. By measuring strain—the amount of deformation a material experiences when subjected to forces such as tension, compression, or bending—extensometers provide critical data needed for understanding material properties. These measurements are essential in determining characteristics like yield strength, tensile strength, and elasticity. Without accurate strain data, engineers and scientists would struggle to predict how materials will perform in real-world applications, potentially compromising safety and performance standards.
In laboratory settings, extensometers are commonly used in tensile tests, where a sample material is pulled until it breaks. The extensometer measures the elongation of the sample throughout the test, allowing for a detailed stress-strain curve to be plotted. This curve is fundamental for comparing materials or validating material specifications. The precision and consistency of extensometers make them indispensable for researchers aiming to develop new materials or improve existing ones.
Types of Extensometers and Their Applications
There are several types of extensometers designed to suit different testing environments and material types. The selection depends on factors such as the material being tested, the expected strain range, and the nature of the test. Common categories include:
- Contact extensometers – These physically attach to the specimen and are suitable for static tests involving metals and rigid materials.
- Non-contact extensometers – Using technologies like lasers or video, these are excellent for fragile or soft materials that could be damaged by physical contact.
- High-temperature extensometers – Designed for use in furnaces or high-heat conditions, ideal for testing materials in aerospace and automotive industries.
Each type offers unique advantages, allowing users to tailor their measurement approach to the material and test requirements. For instance, non-contact extensometers enable high-precision measurements for delicate specimens such as polymers or composites, where even slight pressure from a contact device might alter the results.
Enhancing Quality Control in Industrial Settings
In industrial environments, quality control relies heavily on accurate and repeatable measurements. Extensometers contribute significantly by ensuring that materials meet specified performance criteria before they are used in manufacturing or construction. This helps prevent costly product failures and ensures compliance with industry standards. By integrating extensometers into automated testing systems, manufacturers can conduct high-throughput testing with minimal human intervention, improving efficiency and consistency.
Key benefits of using extensometers in quality control include:
- Detection of material inconsistencies early in the production process
- Verification of supplier material properties
- Support for compliance with international standards such as ASTM and ISO
With ongoing advancements in sensor technology and data acquisition systems, extensometers now offer real-time feedback and integration with digital quality management systems. This connectivity enhances traceability and supports data-driven decision-making in production environments.
Improving Accuracy and Repeatability in Research
In research and development, where precision is critical, extensometers provide the high-resolution data needed for material characterization. Whether studying new alloys or testing composite materials for aerospace applications, researchers depend on extensometers to deliver consistent, replicable results. This is particularly important when validating computational models or conducting long-term fatigue tests.
Modern extensometers are often equipped with advanced features such as:
- Digital output for seamless data integration
- High-frequency response for dynamic testing
- Minimal signal noise for improved measurement clarity
These capabilities support a wide range of experimental setups, from simple tensile tests to complex multi-axial loading scenarios. The precision offered by extensometers helps researchers understand the nuanced mechanical behavior of materials under various loading conditions, leading to innovations in product design and materials science.
Considerations for Selecting an Extensometer
Choosing the right extensometer involves evaluating the specific needs of the testing application. Factors such as gauge length, measurement range, sensitivity, and environmental conditions must be considered. For example, tests conducted at high temperatures require extensometers with materials and designs that can withstand thermal expansion without compromising accuracy.
Some key factors to consider include:
- Material type and geometry
- Expected strain range and resolution requirements
- Test environment (temperature, humidity, vibration)
- Data acquisition and processing capabilities
Additionally, ease of use and maintenance are important, especially in high-volume testing labs where throughput is essential. Investing in flexible and modular extensometer systems can help organizations adapt to changing testing needs over time, maximizing both performance and cost-efficiency.
Conclusion
Extensometers are critical instruments for ensuring accuracy, consistency, and reliability in both material testing and quality control. Their ability to provide precise strain measurements under various conditions makes them a cornerstone of modern engineering and manufacturing processes. Whether in a research lab developing new materials or on a production line verifying product quality, extensometers contribute to informed decision-making and improved material performance. For professionals involved in materials science, engineering, and quality assurance, integrating extensometers into their workflows is a practical step toward achieving greater reliability and efficiency in their work.