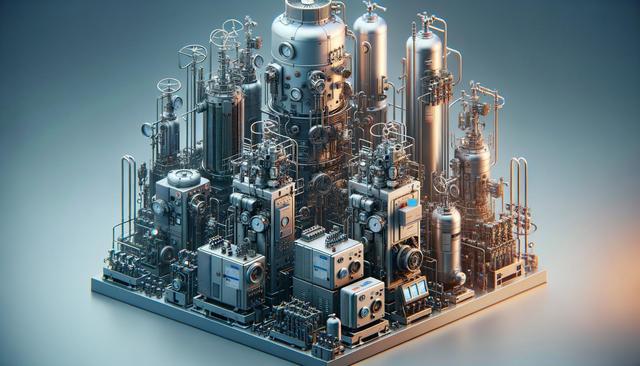
Compare High Pressure Nitrogen Compressors options for Industrial Use
Understanding the Role of High Pressure Nitrogen Compressors in Industry
High pressure nitrogen compressors play a critical role in various industrial applications, including oil and gas operations, electronics manufacturing, food packaging, and metal processing. These compressors are designed to deliver nitrogen at pressures significantly higher than standard compressors, often reaching up to 6,000 psi or more depending on the application. Their primary function is to provide a consistent and reliable flow of compressed nitrogen to support processes that demand inert gas environments, high-pressure purging, or pressurization.
Industries rely on nitrogen for its non-reactive nature, making it ideal for tasks where oxygen could pose a risk of oxidation or combustion. The use of high pressure nitrogen compressors ensures that this gas is delivered efficiently and safely, especially in high-demand settings. Selecting a suitable compressor requires understanding not only the required pressure levels but also the duty cycle, flow rate, and compatibility with existing infrastructure. These factors contribute significantly to operational reliability and energy efficiency.
Key Features to Consider When Comparing Compressor Options
When evaluating high pressure nitrogen compressors for industrial use, several features distinguish one model from another. These features directly impact performance, maintenance needs, and long-term cost-effectiveness.
Key considerations include:
- Maximum Operating Pressure: Ensure the compressor can meet or exceed the pressure requirements of your application.
- Flow Rate: Measured in standard cubic feet per minute (SCFM), this dictates how much nitrogen can be delivered over time.
- Cooling Systems: Compressors may use air or water cooling. The right choice depends on ambient conditions and usage frequency.
- Lubrication Type: Oil-free compressors are often preferred in industries where contamination must be avoided, such as food and electronics.
- Control Systems: Digital controls and remote monitoring can enhance operational efficiency and reduce downtime.
These features should be carefully matched with your operational needs to ensure reliable, long-term performance. Industrial environments often demand robust construction, so it’s also wise to consider the materials and build quality of the compressor unit.
Comparing Compressor Technologies: Reciprocating vs. Scroll vs. Booster Types
High pressure nitrogen compressors come in various technological designs, each with its advantages. The most common types include reciprocating compressors, scroll compressors, and booster compressors.
Reciprocating Compressors are piston-driven and are known for their ability to deliver extremely high pressures. They are durable and suitable for intermittent use where high pressure is needed in short bursts. However, they often require more maintenance due to the number of moving parts.
Scroll Compressors are quieter and more compact. Although they generally offer lower maximum pressures than reciprocating models, they are highly efficient and suitable for continuous operation in environments where noise and space are concerns.
Booster Compressors are used to elevate the pressure of nitrogen that has already been compressed to a moderate level. These are ideal when an existing nitrogen generation system is in place but requires a higher pressure output for specific applications.
Choosing the right technology depends on the required duty cycle, pressure range, and available infrastructure. Each type serves a unique set of use cases within industrial processes.
Energy Efficiency and Operational Costs
Energy efficiency is a crucial factor in choosing a high pressure nitrogen compressor, especially for facilities running large systems continuously. Compressors with energy-saving features can significantly reduce operational costs over time. Variable speed drives (VSDs), for instance, adjust the compressor motor speed to match the nitrogen demand, avoiding unnecessary energy use.
Additionally, maintenance schedules and component durability affect the total cost of ownership. Compressors that feature easy-access service points and modular components simplify preventative maintenance and reduce downtime. Some models also integrate advanced diagnostics and predictive maintenance alerts, which help prevent costly failures and extend equipment lifespan.
When comparing models, it’s important to review:
- Energy consumption per unit of gas delivered
- Total lifecycle cost including maintenance, parts, and downtime
- Warranty terms and manufacturer support
These considerations are especially relevant for facilities with tight energy budgets or a focus on sustainability, making energy-efficient compressors a strategic investment.
Applications and Industry Suitability
Different industries require specific compressor setups based on their operational environments. In the oil and gas sector, for instance, high pressure nitrogen compressors are often used for enhanced oil recovery and pipeline purging. These settings need rugged units capable of handling harsh conditions and remote operation.
In food and beverage manufacturing, nitrogen is used for packaging to extend shelf life and maintain product quality. These applications demand oil-free compressors to avoid contamination. Electronics manufacturing also requires a clean and dry nitrogen supply to prevent oxidation and improve product integrity.
Common industries that benefit from high pressure nitrogen compressors include:
- Oil and gas exploration and processing
- Pharmaceutical and chemical production
- Food and beverage packaging
- Metal fabrication and laser cutting
- Semiconductor and electronics manufacturing
Understanding the specific requirements of your industry will help in selecting a compressor that meets regulatory standards and operational expectations. It also ensures smoother integration with existing systems and processes.
Conclusion: Choosing the Right High Pressure Nitrogen Compressor
Investing in a high pressure nitrogen compressor requires a thorough understanding of your industrial needs, the available compressor technologies, and long-term operational costs. By carefully comparing features such as pressure capacity, flow rate, cooling types, and energy efficiency, businesses can identify options that align with their performance requirements and budget. Whether your priority is consistent nitrogen delivery, low maintenance, or energy savings, there are several top-rated models available that offer dependable performance in demanding environments.
Ultimately, the right choice depends on balancing technical specifications with application demands. Collaborating with knowledgeable vendors and reviewing case studies or user feedback can also provide valuable insights during the selection process. A well-matched compressor not only enhances operational efficiency but contributes to safer and more reliable industrial workflows.