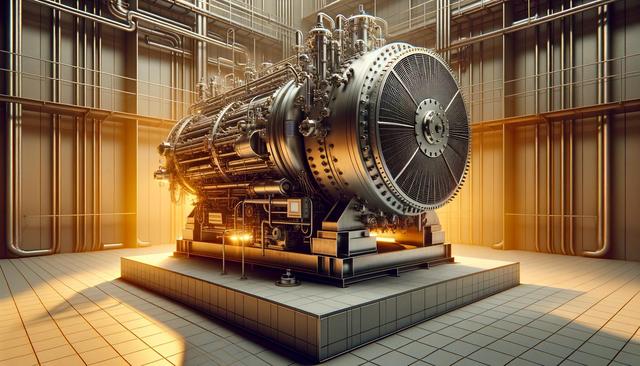
High Temperature Industrial Heat Pumps for Demanding Applications
Meeting the Demands of High-Temperature Industrial Processes
In industries where thermal processes are central to operations, maintaining efficiency at elevated temperatures is a challenge. High temperature industrial heat pumps are engineered specifically to address these demands, offering a reliable solution for sectors such as chemicals, food processing, pharmaceuticals, and heavy manufacturing. These systems are capable of delivering heat at temperatures above 100°C, with some models reaching up to 160°C or more. This makes them suitable for processes such as drying, pasteurization, distillation, and industrial washing — all of which require consistent and high-grade thermal energy.
Unlike conventional heat pumps, high temperature variants are built with robust components that can withstand harsh operating environments. Their design often includes advanced compressors, high-pressure refrigerants, and corrosion-resistant materials. As a result, they are not only capable of managing extreme heat but also offer improved durability and reduced maintenance needs, making them a practical choice for continuous industrial operation.
Industries benefit from these systems by achieving:
- Reduced reliance on fossil fuels
- Lower greenhouse gas emissions
- Improved process stability and control
- Long-term operational cost savings
These advantages highlight the growing role of such technologies in industrial decarbonization efforts and energy transition strategies.
Technology Behind High Temperature Heat Pumps
The core of a high temperature industrial heat pump lies in its thermodynamic cycle, which typically involves a working fluid (refrigerant) that absorbs, compresses, and releases heat. However, operating at high temperatures introduces unique engineering challenges. To overcome these, manufacturers employ specialized refrigerants with high critical temperatures, such as hydrocarbons or hydrofluoroolefins (HFOs), and use multi-stage compression systems to maintain performance across a wide temperature range.
Additionally, modern units often incorporate innovative features such as:
- Oil-free magnetic bearing compressors for enhanced efficiency
- Integrated heat recovery systems to maximize energy utilization
- Smart control systems for precise temperature regulation
These technical enhancements contribute to better adaptability in processes where thermal loads fluctuate or where high-precision heating is critical. Furthermore, the continuous improvement in component materials and control algorithms ensures that these systems remain reliable even under intensive, round-the-clock operation.
Applications Across Industrial Sectors
High temperature industrial heat pumps are gaining traction across various sectors due to their ability to reduce carbon footprints and operational costs. In the chemical industry, they are used to supply process heat for reactions and separations. In food and beverage manufacturing, they enable hygienic processing steps such as sterilization and drying with minimal energy input. Similarly, in pulp and paper, textile, and pharmaceutical sectors, these systems provide stable and clean thermal energy needed for delicate and continuous processes.
Some common high-demand applications include:
- Steam generation for process heating
- Hot water production above 120°C
- Evaporation and concentration systems
- High-temperature air heating for drying operations
In each of these areas, the integration of high temperature heat pumps not only contributes to sustainability goals but also enhances productivity by reducing downtime and improving temperature consistency.
Energy Efficiency and Environmental Impact
One of the most compelling benefits of high temperature industrial heat pumps is their energy efficiency. These systems can achieve a coefficient of performance (COP) significantly higher than traditional boiler systems, especially when operated with renewable electricity. By extracting ambient or waste heat and upgrading it to usable process temperatures, they minimize energy consumption while maximizing output.
Moreover, the environmental impact is notably reduced when these systems replace fossil-fuel-based heating. Lower CO2 emissions, decreased air pollution, and improved energy sourcing are all achievable outcomes. In regions with carbon pricing or regulatory incentives, companies adopting heat pump technology can also benefit from cost reductions and compliance advantages.
Key environmental benefits include:
- Reduction of direct combustion emissions
- Support for electrification of heat
- Enhanced integration with renewable energy sources
As sustainability becomes a central focus for industrial operations worldwide, high temperature heat pumps offer a viable and forward-looking solution.
Integration and Considerations for Implementation
Integrating high temperature heat pumps into existing industrial infrastructure requires careful planning. Factors such as existing heat sources, space availability, process compatibility, and utility connections all play a role in determining feasibility. A thorough assessment is crucial to ensure successful implementation and to maximize return on investment.
Important steps in the integration process include:
- Conducting an energy audit to identify heat demand profiles
- Evaluating the temperature lift required for target processes
- Assessing compatibility with existing heating systems
- Planning for maintenance and operational training
In many cases, heat pumps can be integrated alongside existing systems to provide supplemental heating or to preheat process streams, thereby reducing the load on conventional boilers. This hybrid approach allows for a phased transition toward full electrification of industrial heat supply.
Conclusion
High temperature industrial heat pumps represent a transformative technology for sectors with intensive thermal energy needs. By delivering reliable heat at elevated temperatures, these systems enable industries to move toward more sustainable, efficient, and cost-effective operations. As energy markets evolve and decarbonization becomes more urgent, the role of advanced heat pump technologies will likely expand, offering industries a resilient path forward in meeting both performance and environmental targets.