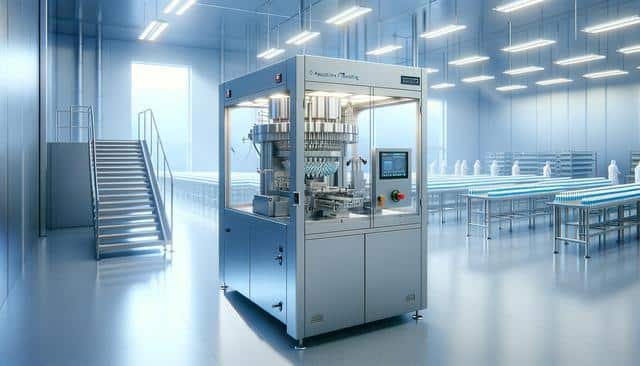
Capsule Filling Machines: Accurate Solutions for Pharma Manufacturing
Understanding the Role of Capsule Filling Machines in Pharma
Capsule filling machines have become a crucial component in modern pharmaceutical manufacturing. These machines are designed to automate the process of filling empty capsules with various types of pharmaceutical substances, such as powders, granules, or pellets. The use of capsule filling machines minimizes human error, enhances consistency in dosage, and meets the stringent hygiene standards required in the industry. As pharmaceutical companies grow and diversify their product lines, the need for efficient and scalable capsule filling solutions continues to rise.
By automating a traditionally manual process, these machines help manufacturers achieve higher throughput while maintaining strict compliance with regulatory guidelines. Precision and repeatability are at the core of capsule filling operations, ensuring that each batch meets exact dosage specifications. This level of accuracy supports not only product quality but also patient safety and satisfaction. As a result, capsule filling machines are integral to maintaining the integrity of pharmaceutical production lines.
Types of Capsule Filling Machines and Their Applications
There are several types of capsule filling machines available on the market, each designed for specific production requirements. Broadly, they fall into two categories: manual and automatic machines. Manual capsule fillers are typically used for small-batch production or research and development purposes, while automatic machines are suited for large-scale manufacturing.
Automatic capsule fillers can be further divided into semi-automatic and fully automatic models. These machines vary in their features, such as:
- Production speed
- Capsule size compatibility
- Filling material type (powder, granules, pellets)
- Level of automation and user interface
Each machine type serves a unique role within the pharma manufacturing landscape. For instance, semi-automatic machines offer a balance between control and automation, making them ideal for mid-sized enterprises. Fully automatic machines, on the other hand, are engineered to handle high-volume production, often operating continuously with minimal downtime.
Accuracy and Efficiency in Capsule Filling Processes
One of the key advantages of using capsule filling machines is the high level of accuracy they offer. This precision is vital in pharmaceutical production, where even minor deviations in dosage can impact the efficacy and safety of the medication. Modern machines come equipped with advanced features such as programmable logic controllers (PLCs), servo motors, and sensors that monitor the filling process in real-time.
These features help ensure:
- Consistent capsule weights
- Reduced rejection rates
- Minimized material waste
- Improved batch traceability
Efficiency is also a critical factor. The ability to produce thousands of capsules per hour with minimal operator intervention translates to lower labor costs and higher productivity. Furthermore, the modular design of many machines allows for quick changeovers between different capsule sizes or formulations, enhancing operational flexibility.
Hygiene and Contamination Control
In pharmaceutical manufacturing, maintaining a sterile and contamination-free environment is non-negotiable. Capsule filling machines are built to support cleanroom standards, often featuring stainless steel construction, enclosed filling systems, and easy-to-clean components. These design elements are essential for preventing cross-contamination and ensuring that each capsule meets regulatory safety standards.
Many machines also incorporate features such as:
- Dust extraction systems
- HEPA filters
- Anti-static materials
- Sealed dosing stations
Regular cleaning and sterilization cycles are also streamlined through tool-free disassembly and CIP (Clean-in-Place) systems. These features not only enhance hygiene but also support compliance with Good Manufacturing Practices (GMP) and other regulatory frameworks.
Scalability and Integration in Modern Facilities
As pharmaceutical companies aim to scale their operations, capsule filling machines must adapt to growing production demands. Modern machines are designed with scalability in mind, offering features that allow seamless integration into existing production lines. This includes compatibility with upstream and downstream equipment such as capsule polishers, checkweighers, and packaging systems.
Advanced machines also support data integration through Manufacturing Execution Systems (MES), enabling real-time monitoring and data logging. This connectivity allows manufacturers to:
- Track production metrics
- Monitor machine performance
- Ensure compliance with quality standards
- Optimize maintenance schedules
Scalability ensures that pharmaceutical manufacturers can respond quickly to market demands without compromising on quality or efficiency. Whether producing a small batch for clinical trials or scaling up for mass-market distribution, capsule filling machines offer a reliable and adaptable solution.
Conclusion: Reliable Solutions for Evolving Pharma Needs
For pharmaceutical manufacturers, capsule filling machines represent a dependable and efficient solution for meeting the industry’s evolving needs. These machines offer a combination of precision, speed, hygiene, and scalability that supports both operational goals and regulatory compliance. By integrating advanced features and automation, they help streamline production and ensure that each capsule meets the highest quality standards. As the demand for pharmaceutical products continues to grow, investing in accurate and reliable capsule filling technology is an essential step toward sustainable and effective manufacturing.