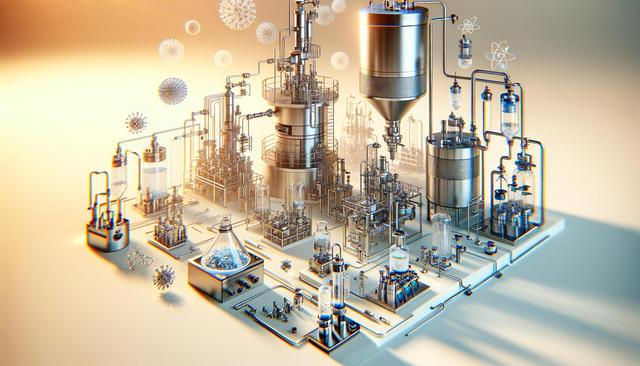
Chemical Dosing Systems: Accurate Dispensing for Process Control
Understanding the Role of Chemical Dosing Systems
Chemical dosing systems are integrated solutions designed to introduce specific amounts of chemicals into process streams with high precision. These systems are widely used across industries such as water treatment, food processing, pharmaceuticals, and manufacturing, where maintaining a consistent chemical balance is critical for process efficiency and product quality. By automating the measurement and injection of chemicals, dosing systems help reduce manual errors, minimize waste, and support compliance with environmental and safety regulations.
The basic components of a chemical dosing system typically include chemical storage tanks, dosing pumps, control units, and sensors. Together, these components ensure that chemicals are dispensed at the right time and in the right amount. This level of control is essential for avoiding overuse or underuse of chemicals, both of which can lead to inefficiencies or compromised outcomes. For example, in water treatment, improper dosing could result in either insufficient disinfection or excessive chemical residues.
Moreover, chemical dosing systems can be tailored to meet the specific needs of an application, allowing for scalability and adaptability. Whether it’s a small-scale laboratory setup or a large industrial facility, these systems can be configured to handle different flow rates, chemical viscosities, and dosing frequencies with accuracy.
Precision and Process Control Advantages
The central benefit of chemical dosing systems lies in their ability to enhance process control through precise chemical delivery. This precision ensures that process conditions remain stable and predictable, which is crucial for maintaining consistent product quality and operational efficiency. Automated dosing minimizes the variability that can arise from manual handling, particularly in high-throughput or continuous-flow operations.
Industries that rely on chemical reactions for their core processes benefit significantly from accurate dosing. These systems allow for:
- Consistent product quality and reduced batch variability
- Improved reaction control and yield optimization
- Minimized risk of overdosing and associated safety hazards
- Lower chemical consumption and environmental impact
Advanced dosing systems often incorporate feedback control mechanisms, where real-time data from process sensors adjust the dosing rate dynamically. This closed-loop control ensures that the chemical balance is maintained even as conditions change, leading to more resilient and adaptive operations.
Integration with Automation and Monitoring Technologies
Modern chemical dosing systems are increasingly integrated with digital automation and monitoring technologies to further enhance functionality. Programmable logic controllers (PLCs), human-machine interfaces (HMIs), and internet-of-things (IoT) devices can be used to monitor system performance, track chemical usage, and alert operators to potential issues. This integration allows for more efficient maintenance, better resource planning, and improved system diagnostics.
Some common features of automated dosing systems include:
- Remote monitoring and control through networked interfaces
- Data logging for traceability and compliance reporting
- Alarm systems for leak detection or dosing anomalies
- Predictive maintenance capabilities using sensor data
These features not only support operational efficiency but also ensure safety and regulatory adherence. By leveraging automation, facilities can reduce labor costs, minimize downtime, and make more informed decisions based on real-time data insights.
Applications Across Various Industries
Chemical dosing systems are used in a wide range of industries where precision and consistency are vital. In water and wastewater treatment, they help maintain correct pH levels, disinfect water sources, and remove contaminants. In the food and beverage industry, they are essential for flavoring, preservation, and sanitation processes. Pharmaceutical manufacturing relies on accurate dosing to ensure formulation integrity and compliance with health standards.
Other sectors also benefit from these systems, including:
- Power generation – for boiler feedwater conditioning
- Oil and gas – for corrosion inhibition and demulsification
- Pulp and paper – for bleaching and process chemical control
- Textile – for dyeing and finishing treatments
Each industry has unique requirements, and dosing systems can be customized accordingly. Factors such as chemical compatibility, temperature resistance, and system footprint are considered during the design phase to ensure efficient integration into existing processes.
Maintaining and Optimizing Dosing System Performance
To maintain high performance and reliability, chemical dosing systems require regular maintenance and calibration. Ensuring that pumps, valves, and sensors are functioning correctly is key to avoiding dosing inaccuracies or system failures. Scheduled inspections and parts replacements can prevent costly downtime and extend the lifespan of the equipment.
Best practices for maintaining dosing systems include:
- Routine calibration of dosing pumps and flow meters
- Cleaning and flushing of chemical lines to prevent buildup
- Inspection of seals and connections for leaks
- Software updates for control systems and interfaces
Additionally, training operators on system usage and maintenance protocols plays a critical role in sustaining performance. A well-maintained system not only ensures accurate dosing but also supports safety and regulatory compliance in sensitive industrial environments.
Conclusion: Enhancing Efficiency Through Accurate Chemical Dispensing
For industries that depend on precise chemical applications, chemical dosing systems offer a reliable and efficient solution. By improving control, reducing waste, and integrating with modern automation tools, these systems support sustainable and cost-effective operations. Organizations that invest in well-designed and properly maintained dosing systems can expect improved product quality, compliance with environmental standards, and greater operational resilience. Whether in water treatment, pharmaceuticals, or manufacturing, accurate chemical dispensing continues to be a cornerstone of effective process control.