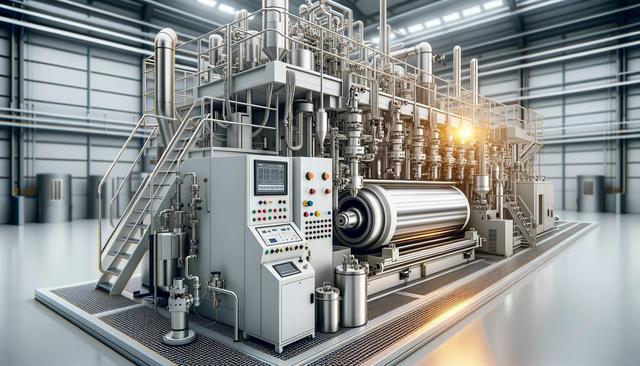
Coating Machine Solutions: Enhancing Surface Treatment Efficiency
Understanding the Role of Coating Machines in Surface Treatment
In industrial manufacturing and processing, surface treatment is a critical step that directly influences the performance, longevity, and appearance of materials. Coating machines have become essential tools in this process, enabling industries to apply protective and functional layers to a wide range of surfaces. Their primary function is to deliver uniform coatings that enhance resistance to corrosion, abrasion, and environmental damage. As industries evolve to meet higher standards of quality and efficiency, the role of coating machine solutions has expanded significantly. These machines not only improve the aesthetics of products but also contribute to their mechanical and chemical stability.
One of the outstanding advantages of modern coating machines is their ability to handle various coating materials such as powders, liquids, and films. By adjusting parameters like speed, temperature, and pressure, operators can achieve optimal coverage with minimal waste. This level of control ensures consistency across batches, which is essential in sectors like automotive, electronics, packaging, and pharmaceuticals.
Key Types of Coating Machine Solutions
Different industries require different coating technologies depending on the nature of the substrate and the function of the coating. As a result, several types of coating machines have been developed to address specific requirements. Common types include:
- Roll Coaters: Ideal for flat surfaces, providing an even application of liquid coatings.
- Spray Coaters: Used for complex geometries and 3D objects, offering flexibility in coverage.
- Dip Coaters: Suitable for batch processes and immersion applications.
- Slot Die Coaters: Deliver high precision for thin film coatings, commonly used in electronics.
Each machine type offers unique advantages depending on the desired outcome. For example, spray coating can be a practical solution for irregular shapes, while roll coating is better suited for continuous sheet materials. Understanding these distinctions helps manufacturers select equipment that aligns with their production goals and material properties.
Enhancing Efficiency Through Automation and Integration
Modern coating machines are increasingly designed with automation in mind to support complex production environments. Automated systems reduce the need for manual intervention, thus minimizing human error and improving safety. Additionally, integrating coating machines with upstream and downstream processes—such as drying, curing, and inspection—can significantly boost overall production efficiency.
Features that contribute to enhanced efficiency include:
- Programmable logic controllers (PLCs) for precise process control
- Real-time monitoring systems for quality assurance
- Energy-efficient components that reduce operational costs
- Modular designs that allow for easy maintenance and upgrades
By investing in advanced coating machine solutions, companies can achieve faster cycle times, higher throughput, and reduced material waste—factors that are critical for competitive manufacturing.
Applications Across Diverse Industries
Coating machines are widely used in industries where product performance and durability are crucial. In the automotive sector, for instance, coating systems are used to apply anti-corrosion layers to chassis components. In electronics, ultra-thin coatings protect circuit boards from moisture and contaminants. Similarly, in the medical field, devices often receive biocompatible coatings to ensure safety and functionality.
Some notable industrial applications include:
- Protective coatings for metal parts in construction and infrastructure
- Barrier films on packaging materials to extend shelf life
- Decorative finishes in consumer electronics and home appliances
- Functional layers in photovoltaic panels and batteries
The adaptability of coating machines to different environments and technical requirements underscores their value in modern production ecosystems.
Sustainability and Future Trends in Coating Technologies
As sustainability becomes a core objective across industries, coating machine technologies are evolving to reduce environmental impact. Many manufacturers are transitioning to water-based and solvent-free coatings that emit fewer volatile organic compounds (VOCs). In parallel, machines are being designed to operate more efficiently, using less energy and material while maintaining high-quality output.
Emerging trends in coating solutions include:
- Digital control systems for precise formulation and application
- Use of eco-friendly coating materials
- Advanced analytics for predictive maintenance
- Integration with Industry 4.0 smart manufacturing platforms
These innovations not only support environmental goals but also open up new possibilities for customized and responsive production processes. As such, businesses that embrace these advancements are better positioned to meet regulatory standards and customer expectations.
Conclusion: Investing in Smart Coating Solutions
For companies aiming to enhance surface treatment efficiency, investing in the right coating machine solutions offers both immediate and long-term benefits. Whether the goal is to improve product durability, streamline production, or meet sustainability targets, modern coating technologies provide the precision and adaptability needed in today’s competitive landscape. With options tailored to various applications and continuous advancements in automation and material science, coating machines remain a foundational element of high-performance manufacturing.