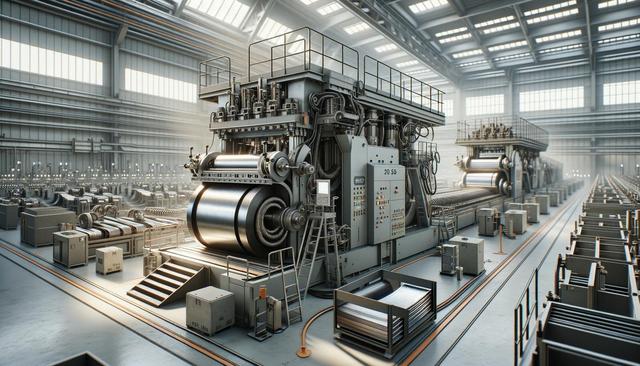
Coil Forming Machines: Precision Shaping for Industrial Coils
Understanding the Role of Coil Forming Machines in Industry
Coil forming machines are integral to the production process of a wide range of electrical and electromechanical devices. These machines are engineered to shape and wind wire into precise coil structures that meet the specifications required for components such as transformers, electric motors, inductors, and solenoids. Their ability to deliver consistent and repeatable coil designs ensures that manufacturers can produce reliable products that perform efficiently in demanding industrial environments. By automating the shaping process, these machines also reduce manual labor and minimize the risk of human error, which is particularly important in applications where precision is non-negotiable.
The versatility of coil forming machines makes them suitable for use across multiple sectors, including automotive, aerospace, power generation, and telecommunications. Each application may require different types of coils—ranging from flat and rectangular to round and multi-layered—depending on the desired electromagnetic properties. The machines are designed to accommodate these variations with adjustable tooling and programmable controls, enhancing their adaptability and usefulness in diverse production settings.
Precision Engineering for Consistent Coil Quality
One of the primary benefits of coil forming machines lies in their precision engineering. These machines are typically equipped with digital control systems, servo motors, and tension management mechanisms that allow operators to fine-tune every aspect of the coil forming process. This level of control ensures uniformity across production batches and reduces the likelihood of defects that could compromise the performance of the final product.
Key features contributing to precision include:
- Automated wire feeding and tension control systems
- Programmable coil dimensions and winding patterns
- Integrated quality monitoring tools
- Data logging for process traceability
With these components working in tandem, manufacturers can maintain tight tolerances and produce coils that meet stringent industry standards. This is particularly important in applications where electrical efficiency, heat distribution, and magnetic field consistency are critical factors.
Applications Across Transformer and Motor Manufacturing
Coil forming machines are widely used in the manufacturing of transformers and motors, where the integrity of the coil directly impacts the performance and durability of the equipment. In transformers, coils must be precisely wound to ensure optimal electromagnetic coupling and minimal energy loss. In motors, the coil geometry influences torque, speed, and overall efficiency.
These machines support various coil types used in:
- Power transformers
- Distribution transformers
- AC and DC motors
- Servo motors
- Step motors
For each of these applications, the accuracy of the winding process is paramount. Coil forming machines help manufacturers achieve this by offering programmable settings that can be tailored to specific coil designs. This not only improves the final product but also reduces waste and increases production speed, contributing to more efficient manufacturing operations.
Technological Advancements and Automation
Recent advances in automation and digital technology have significantly enhanced the capabilities of coil forming machines. Modern units often feature touchscreen interfaces, real-time diagnostics, and network connectivity, enabling integration with smart factory systems. These improvements not only streamline the production process but also provide valuable data insights that can be used for continuous improvement.
Some of the innovative technologies now commonly found in coil forming machines include:
- IoT-enabled monitoring systems
- AI-driven quality control algorithms
- Remote operation capabilities
- Automated tool change systems
These features allow manufacturers to adapt quickly to changing production needs and ensure that their equipment remains efficient and reliable. As industries continue to embrace digital transformation, the role of intelligent coil forming machines is expected to grow even more central in high-precision manufacturing environments.
Selecting the Right Coil Forming Machine for Your Needs
Choosing the appropriate coil forming machine depends on several factors, including the type of coil being produced, the desired production volume, and the specific quality standards of the application. Manufacturers must consider machine specifications such as wire size range, coil diameter capabilities, speed, and compatibility with different winding patterns.
To make an informed selection, it’s advisable to assess the following:
- Required coil geometries and configurations
- Material types and wire gauges
- Production throughput requirements
- Available customization options
- Service and support availability
Working with a knowledgeable equipment provider can help ensure that the machine selected aligns with both current operational needs and future scalability. Additionally, considering the ease of maintenance and availability of replacement parts can contribute to long-term cost savings and minimized downtime.
Conclusion: Enhancing Production with Coil Forming Precision
For industries reliant on precise electrical components, coil forming machines represent a critical investment in quality and efficiency. Their ability to produce consistent, high-performance coils supports the functionality of essential devices such as transformers and motors. With ongoing advancements in automation and digital integration, these machines continue to evolve, offering manufacturers new ways to optimize production and maintain competitive standards. Organizations seeking to enhance their coil fabrication capabilities should carefully evaluate their operational goals and select equipment that offers the flexibility, precision, and reliability required for long-term success.