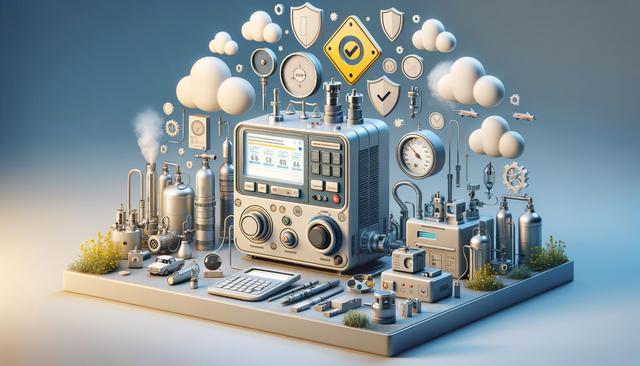
Ensuring Safety: The Role of Gas Detector Calibration Machines in Regulatory Compliance
The Importance of Accurate Gas Detection
In environments where hazardous gases are present, the ability to detect and measure gas concentrations precisely is critical. Accurate gas detection helps prevent health hazards, explosions, and environmental damage. A Gas Detector Calibration Machine plays a central role in ensuring that gas detectors function correctly by verifying and adjusting their sensor readings. This process is essential for maintaining workplace safety and fulfilling legal and environmental obligations. Without regular calibration, gas detectors may produce false readings—either failing to detect dangerous levels or triggering unnecessary alarms—both of which can lead to serious consequences.
Industries such as oil and gas, chemical manufacturing, mining, and waste treatment rely heavily on dependable gas detection systems. These sectors are often required to comply with strict safety regulations, and the use of properly calibrated detectors is a fundamental part of that compliance. Calibration not only helps in identifying potential dangers but also ensures that safety protocols are based on accurate data.
Understanding Gas Detector Calibration Machines
A Gas Detector Calibration Machine is a specialized device designed to test and adjust gas detection instruments. The calibration process involves exposing the detector to a known concentration of calibration gas to evaluate its response. If the detector’s readings are outside acceptable limits, the calibration machine allows for necessary adjustments to bring the readings back in line.
Key components of a gas detector calibration system typically include:
- Calibration gas cylinders with certified gas concentrations
- Flow regulators to control gas flow during calibration
- Automated or manual calibration interfaces
- Software for data logging and compliance tracking
Using a calibration machine helps maintain consistency in detector performance, especially in facilities where environmental conditions or gas exposure levels fluctuate. Regular calibration ensures that the equipment continues to meet the required standards over time.
Regulatory Compliance and Industry Standards
Many regional and international safety standards mandate regular calibration of gas detection equipment. Regulatory bodies such as occupational safety authorities often require documentation proving that gas detectors are calibrated according to the specified schedule. Failing to comply with these standards can result in penalties, operational shutdowns, or increased liability in the event of an incident.
Gas Detector Calibration Machines help businesses meet these regulatory requirements more efficiently. By automating the calibration process and keeping digital records, these machines streamline compliance efforts. Typical standards that influence calibration practices include:
- Occupational safety regulations
- Environmental monitoring protocols
- Fire and explosion prevention standards
- ISO and ANSI certification requirements
Incorporating calibration into regular maintenance routines not only meets compliance needs but also contributes to a safer and more reliable work environment.
Benefits for Operational Efficiency and Safety
Beyond compliance, the use of Gas Detector Calibration Machines contributes significantly to operational efficiency. Accurate detectors help minimize downtime due to false alarms and reduce the need for emergency responses. This, in turn, improves productivity and reduces operational costs.
Other benefits include:
- Extended lifespan of gas detection equipment through proper maintenance
- Reduced risk of undetected gas leaks
- Improved confidence among workers and safety officers
- Better planning and execution of maintenance schedules
When calibration is part of a broader safety management system, it reinforces a culture of accountability and diligence. Employees are more likely to trust equipment that is regularly maintained and verified, encouraging adherence to safety practices.
Choosing the Right Calibration Approach
Different industries have varying needs when it comes to gas detector calibration. Factors such as the type of gases monitored, the frequency of exposure, and the criticality of the application influence the calibration method. Some organizations may opt for manual calibration setups, while others invest in fully automated solutions for higher efficiency and consistency.
When selecting a calibration machine, considerations include:
- Compatibility with existing gas detection equipment
- Ease of use and training requirements
- Accuracy and repeatability of the calibration process
- Data management and reporting capabilities
Customizing the calibration approach to suit operational needs not only enhances safety but also delivers long-term value through reliable performance and reduced maintenance issues. Investing in a Gas Detector Calibration Machine that aligns with organizational goals is a strategic decision that supports both compliance and operational excellence.
Conclusion: Supporting Safe and Compliant Workplaces
Ensuring the accuracy of gas detection systems is not just a technical requirement—it is a foundational element of workplace safety and regulatory compliance. Gas Detector Calibration Machines serve as a crucial tool in maintaining this accuracy, helping industries meet legal obligations and uphold high safety standards. By integrating regular calibration into safety protocols, organizations can better protect their personnel, assets, and reputation. For businesses operating in high-risk environments, investing in reliable calibration solutions is a proactive step toward building a secure and compliant operational framework.