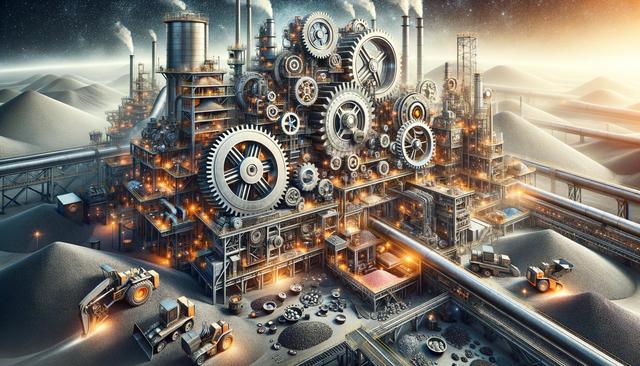
Essential Machinery for Extracting and Refining Iron Ore
Drilling and Blasting Equipment: Initiating the Extraction
The first step in iron ore extraction is uncovering the ore deposits, which often lie beneath layers of rock and soil. To access these ore bodies, mining operations rely on drilling and blasting equipment. Rotary drills and down-the-hole hammer drills are among the most commonly used types of machinery for creating boreholes where explosives are inserted. Once the drilling is complete, controlled blasting breaks the rock into manageable sizes for transportation.
This phase requires precision to ensure minimal waste and reduce environmental impact. Key machinery includes:
- Rotary blast hole drills for large-scale ore bodies
- Hydraulic drills for smaller or more precise drilling operations
- Bulk explosive trucks for on-site mixing and delivery of blasting agents
The choice of drilling and blasting equipment depends on several factors, including ore hardness, depth, and the surrounding geology. Properly executed blasting not only improves downstream processing efficiency but also reduces wear on crushing equipment later in the process.
Crushing and Screening Systems: Preparing the Ore
After blasting, the fragmented ore must be transported to a primary crusher. This stage involves reducing the large rocks into smaller, more uniform pieces. Primary crushers, such as jaw crushers or gyratory crushers, are essential for handling the initial size reduction. Following this, secondary and tertiary crushers further refine the ore to the required size for concentration.
Screening systems are used in parallel to separate the crushed ore based on size. Vibrating screens and grizzly feeders help ensure that only appropriately sized material moves forward in the process, while oversized rocks are sent back for further crushing.
Key machinery in this phase includes:
- Jaw crushers for initial size reduction
- Cone or impact crushers for secondary crushing
- Vibrating screens for particle size classification
Efficient crushing and screening not only enhance throughput but also improve the effectiveness of subsequent beneficiation processes.
Beneficiation Equipment: Concentrating the Ore
Once the ore has been appropriately crushed and screened, it moves to the beneficiation stage, where impurities are removed to concentrate the iron content. Beneficiation processes vary depending on the type of ore and desired outcome, but magnetic separation and flotation are two common techniques.
Magnetic separators are highly effective for magnetite ores, using magnetic fields to separate iron-rich particles from waste rock. For hematite ores, gravity separation, flotation cells, and hydrocyclones are often employed to concentrate the ore.
Essential machinery includes:
- Wet and dry magnetic separators for magnetite concentration
- Flotation cells for hematite and low-grade ores
- Thickeners and filters for dewatering concentrated slurry
Effectively concentrating the ore at this stage significantly reduces the energy and resources needed in the reduction and refining stages. It also minimizes transportation costs by reducing the volume of material moved to the next processing site.
Reduction Furnaces and Kilns: Extracting Metallic Iron
In the reduction stage, concentrated iron ore is converted into metallic iron. This is typically done through either a blast furnace or a direct reduction process, depending on the type of ore and available infrastructure. Blast furnaces use coke as both fuel and a reducing agent to transform iron oxide into molten iron, while direct reduction employs natural gas or other reducing gases at lower temperatures.
Important machinery in this stage includes:
- Blast furnaces for large-scale smelting operations
- Rotary kilns and shaft furnaces for direct reduction
- Gas reformers and preheaters for efficient energy use
These systems operate under extremely high temperatures and require rigorous maintenance and monitoring to ensure safety and efficiency. The output is either pig iron or directly reduced iron (DRI), which can be used in steelmaking or further refined to meet specific industrial needs.
Refining and Casting Equipment: Finalizing the Product
The final stage in iron ore processing is refining and casting. This involves removing additional impurities such as carbon, sulfur, and phosphorus from the molten iron to produce various grades of steel or pure iron. Refining typically occurs in basic oxygen furnaces, electric arc furnaces, or induction furnaces, depending on the end product requirements and energy sources available.
Once refined, the molten metal is cast into usable forms such as billets, slabs, or ingots. Continuous casting machines and ingot molds are employed here to shape the metal while it cools and solidifies.
Common machinery in this phase includes:
- Basic oxygen furnaces for high-volume steelmaking
- Electric arc furnaces for recycling and alloying
- Continuous casting machines for efficient shaping
The refining and casting process is where the final properties of the iron or steel are established. It is also one of the most quality-sensitive stages, requiring precise control over temperature, composition, and cooling rates.
Conclusion
Each stage in the extraction and refining of iron ore depends on a range of sophisticated machinery designed to optimize productivity, safety, and environmental performance. From drilling and blasting to refining and casting, the equipment involved plays a critical role in transforming raw iron ore into usable materials for construction, manufacturing, and infrastructure. Understanding the essential machinery used throughout this process helps industry professionals make informed decisions about equipment investment and process design to ensure sustainable and efficient operations.