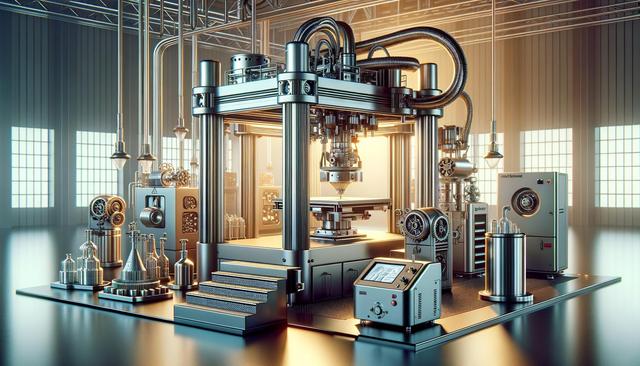
High-Precision 3D Printing Equipment for Industrial Prototyping
Understanding the Role of 3D Printing in Industrial Prototyping
3D printing has become a transformative force in industrial prototyping, offering manufacturers the ability to create detailed and functional prototypes with remarkable accuracy. Unlike traditional methods that often involve lengthy and costly tooling processes, 3D printing streamlines prototyping by allowing direct fabrication from digital models. This approach enables rapid iteration, significantly reducing time-to-market for new products. High-precision 3D printers capable of handling metal and resin materials are particularly valuable for industries such as aerospace, automotive, and medical device manufacturing, where accuracy and material properties are critical.
These advanced printers support the creation of complex geometries and fine details that would be difficult or impossible to achieve using conventional methods. For instance, internal lattice structures, intricate cooling channels, and custom-fit components can be printed with minimal manual intervention. This opens up new possibilities for innovation and customization at the prototyping stage.
Metal vs. Resin 3D Printing: Choosing the Right Tool
The choice between metal and resin 3D printing largely depends on the application and performance requirements of the prototype. Metal 3D printing, also known as direct metal laser sintering (DMLS) or selective laser melting (SLM), is ideal for creating parts that need to endure high mechanical stresses or thermal loads. It’s commonly used for:
- Functional prototypes for mechanical testing
- Tooling components and fixtures
- End-use parts in small production runs
On the other hand, resin-based 3D printing, often performed through stereolithography (SLA) or digital light processing (DLP), excels in producing high-resolution parts with smooth surface finishes. These printers are well-suited for:
- Visual prototypes for design validation
- Dental and medical models
- Small, intricate parts requiring fine detail
Understanding the strengths and limitations of each material type helps manufacturers make informed decisions when selecting equipment for their specific prototyping needs.
High Precision: A Key Differentiator for Industrial Applications
When it comes to industrial prototyping, precision is more than just a desirable feature—it’s essential. High-precision 3D printing equipment ensures dimensional accuracy, repeatability, and surface quality that meet the stringent demands of engineering applications. This level of precision is crucial during product development, where even minor discrepancies can lead to functional failures or increased production costs further down the line.
Modern 3D printers achieve this precision through advanced control systems, high-resolution printing heads, and optimized software that minimizes errors. Features contributing to enhanced precision include:
- Layer thickness control down to microns
- Temperature regulation for consistent material behavior
- Automated calibration and monitoring systems
Such capabilities are particularly important in regulated industries, where prototypes must comply with detailed specifications or undergo rigorous testing and certification processes. Investing in equipment that consistently delivers high precision ultimately improves product quality and reduces the risk of costly redesigns.
Maintenance and Service Plans: Ensuring Long-Term Performance
High-end 3D printing equipment represents a significant investment, making effective maintenance plans a critical component of long-term performance and reliability. Regular maintenance not only extends the lifespan of the equipment but also maintains the consistency and quality of prints. Most manufacturers offer structured maintenance programs that include:
- Scheduled servicing and parts replacement
- Software and firmware updates
- Remote diagnostics and on-site technical support
These plans are designed to minimize downtime and prevent unexpected failures that could disrupt production schedules. Moreover, having access to trained service technicians ensures that issues are addressed promptly and professionally. For industrial users relying on 3D printing for time-sensitive prototyping, this level of support can be a decisive factor in operational efficiency.
It’s also worth considering predictive maintenance features in modern equipment. Using sensors and analytics, these systems can monitor the condition of key components and alert operators before a failure occurs. This proactive approach to equipment care supports continuous operation and reduces the likelihood of unscheduled interruptions.
Integrating 3D Printing into the Prototyping Workflow
Successfully adopting high-precision 3D printing technology involves more than just purchasing equipment. Integrating it into the prototyping workflow requires planning, training, and alignment with existing processes. Teams must be trained on the specific capabilities and limitations of the new systems, and design engineers may need to adapt their models to take full advantage of additive manufacturing techniques.
Key steps for effective integration include:
- Assessing prototyping needs and selecting appropriate equipment
- Establishing digital workflows for CAD to print
- Creating quality control protocols for printed prototypes
- Developing internal expertise or partnering with experienced service providers
Additionally, building a feedback loop between designers, engineers, and machine operators can help refine the use of 3D printing within the organization. Over time, this collaborative approach can lead to optimized designs, faster iterations, and more efficient use of resources. As 3D printing becomes more embedded in the prototyping cycle, companies can gain a competitive edge through faster innovation and improved product development.
Conclusion: A Strategic Choice for Modern Manufacturers
For industrial manufacturers focused on innovation, investing in high-precision 3D printing equipment designed for metal and resin applications is a strategic decision. These tools enable faster prototyping, greater design flexibility, and improved product quality. By understanding the differences between material types, the importance of precision, and the value of robust maintenance plans, organizations can make informed choices that support both current and future prototyping needs. When properly integrated into the design and development process, 3D printing can become a powerful asset in delivering high-performance products to market more efficiently.