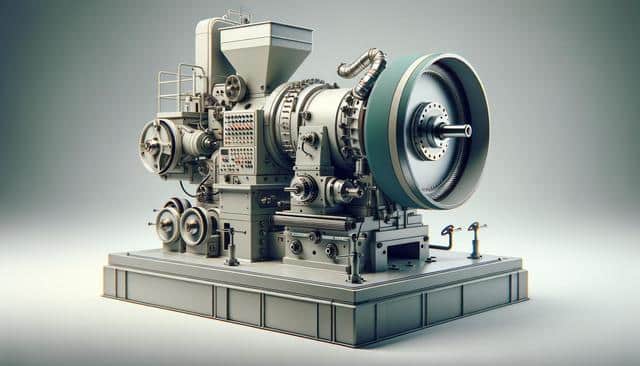
Industrial Grinding Machine: Types, Features & Industry-Specific Uses
Understanding the Core Types of Industrial Grinding Machines
Industrial grinding machines are essential tools in modern manufacturing, enabling precision shaping, surface finishing, and part modification across a range of materials. These machines come in various types, each tailored to specific tasks and industries. The most widely used types include surface grinders, cylindrical grinders, centerless grinders, and tool and cutter grinders. Each type plays a unique role depending on the application. For example, surface grinders are ideal for creating smooth finishes on flat surfaces, while cylindrical grinders are more suited for shaping the outer surfaces of cylindrical objects. Centerless grinders, known for their high throughput, are often used in production lines, and tool and cutter grinders specialize in sharpening and forming cutting tools. Selecting the appropriate type improves efficiency and product quality, particularly in sectors such as aerospace, automotive, and heavy equipment manufacturing.
Key Features That Define Performance and Efficiency
The efficiency and adaptability of industrial grinding machines largely depend on their features. These machines are built to handle heavy-duty tasks while maintaining high precision. Some essential features to consider include:
- Automatic feed mechanisms for consistent material removal
- Variable speed controls to handle different materials and hardness
- High-precision spindles ensuring accurate grinding tolerances
- Advanced coolant systems to reduce heat and maintain dimensional stability
- Digital control panels for programmable operations
Modern grinding machines often integrate CNC (Computer Numerical Control) systems, which enhance accuracy and repeatability. These features are especially valuable in industries requiring strict compliance with dimensional tolerances and surface finishes. Additionally, the use of high-quality abrasive wheels and improved machine rigidity contributes to longer tool life and reduced downtime, making operations more cost-effective and reliable.
Applications Across Key Industries
Industrial grinding machines are used in a variety of industries, each requiring specific capabilities. In the automotive sector, these machines are indispensable for producing engine components, transmission parts, and brake systems with high precision. The aerospace industry relies on grinding machines for manufacturing turbine blades and structural components made from hard-to-machine materials. In the medical field, precision grinding is used to create surgical tools and implants. Heavy industries such as shipbuilding and railway manufacturing also use large-scale grinders for maintaining and fabricating critical components.
Textile and paper manufacturing units use specialized grinding machines to maintain rollers and blades, ensuring smooth production processes. In electronics, ultra-precision grinding machines enable the shaping of delicate components like semiconductors and microchips. The adaptability of grinding machines to different scales and materials makes them valuable assets across these varied sectors.
Choosing the Right Machine for Your Operation
Selecting the right industrial grinding machine depends on several factors, including material type, required surface finish, production volume, and budget. Small-scale operations may benefit from manual or semi-automatic machines, while high-volume production lines typically require CNC-enabled machines for consistency and speed. It is also important to evaluate the compatibility of the machine with existing equipment and workflow processes.
Other considerations include:
- Ease of maintenance and availability of spare parts
- Energy efficiency and environmental impact
- Operator safety features and ergonomic design
- Software compatibility for automated systems
Consulting with equipment suppliers or industry experts can help identify the most suitable model and configuration for specific operational needs. A well-informed choice can lead to significant improvements in productivity, product quality, and overall operational efficiency.
Maintenance and Operational Best Practices
Maintaining an industrial grinding machine properly extends its service life and ensures consistent performance. Routine inspections should focus on wear parts such as grinding wheels, spindles, and drive belts. Regular lubrication of moving parts, alignment checks, and monitoring of coolant systems are also essential to prevent breakdowns and ensure smooth operation.
Training operators in machine-specific procedures and safety protocols is equally important. Best practices include:
- Keeping the work area clean and free from debris
- Using the correct grinding wheel for the material and task
- Monitoring machine performance for signs of imbalance or wear
- Documenting maintenance schedules and repair history
Implementing a preventive maintenance strategy not only minimizes downtime but also enhances workplace safety. Investing in quality tools and adhering to operational guidelines can significantly reduce the risk of accidents and maintain high production standards over time.
Conclusion: Tailoring Grinding Solutions to Industrial Demands
Industrial grinding machines are vital components in numerous manufacturing sectors, offering precision, efficiency, and adaptability. By understanding the various types, features, and industry-specific applications, businesses can make informed decisions that align with their production goals. Whether in aerospace, automotive, medical, or heavy industry, choosing and maintaining the right grinding equipment is key to achieving long-term operational success.