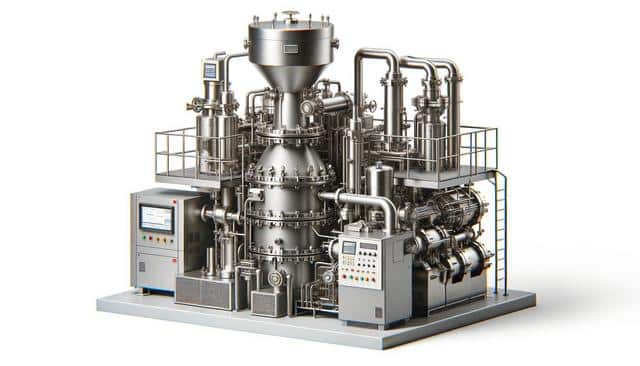
Industrial Homogenizers for Consistent and Reliable Mixing
Understanding the Role of Industrial Homogenizers
Industrial homogenizers are integral to manufacturing processes where consistent texture, stability, and uniformity are critical. These machines work by applying mechanical force to reduce particle sizes and ensure that mixtures are evenly blended. Whether in food production, pharmaceutical formulation, or chemical processing, homogenization plays a pivotal role in improving product quality. The main function of a homogenizer is to break down solids or immiscible liquids into smaller, more uniform particles, allowing for better product structure and performance. This results in smoother textures, prolonged shelf life, and enhanced appearance—qualities that are particularly important in consumer-facing industries.
In sectors like food and beverage, homogenizers are used to ensure products such as sauces, dairy items, and beverages maintain consistent taste and mouthfeel. In pharmaceuticals, they help achieve uniform distribution of active ingredients, which is essential for dosage accuracy. The chemical industry benefits from homogenizers in emulsifying or dispersing reactive components, supporting the creation of stable and effective formulations. Their ability to perform reliably across different batch sizes also makes them valuable tools for both small-scale and large-scale production lines.
Key Features That Support Consistency
The design of industrial homogenizers incorporates several features that contribute to the consistency and reliability of the mixing process. These features are engineered to deliver precise control over the mixing environment, minimizing variability between batches. Some of the most notable elements include:
- High-pressure pumps that force materials through narrow gaps, enabling fine particle reduction
- Adjustable valve systems that allow customization of flow and pressure conditions
- Temperature control units to maintain optimal conditions during processing
- Automated cleaning systems that ensure hygiene and minimize downtime
Such technical specifications allow manufacturers to replicate results with high accuracy, which is particularly important when scaling up production. The combination of mechanical efficiency and automation ensures that every batch meets predefined quality standards, reducing the risk of inconsistencies that can lead to product recalls or customer dissatisfaction. Moreover, many modern homogenizers include data logging and monitoring systems, providing real-time feedback for process optimization and quality assurance.
Applications Across Various Industries
Industrial homogenizers are used across a wide range of industries, each with specific requirements and challenges. In the food industry, they are instrumental in producing homogeneous mixtures that contribute to flavor uniformity and visual appeal. For example, salad dressings, dairy products, and fruit juices all benefit from homogenization to prevent separation and ensure a smooth texture.
In pharmaceuticals, the need for accurate dosing and bioavailability of active ingredients makes homogenization essential. Homogenizers help create nano and micro-emulsions for creams, ointments, and injectable drugs. The chemical industry utilizes these machines in the production of paints, lubricants, and polymers, where consistent dispersion of raw materials is critical. Key applications include:
- Creating stable emulsions for personal care products
- Enhancing solubility and absorption rates in medication
- Preventing sedimentation in liquid chemicals
- Improving the stability of pigment dispersions
This versatility demonstrates the adaptability of industrial homogenizers to a broad spectrum of manufacturing needs, making them indispensable in modern production environments.
Benefits of Consistent and Reliable Mixing
The benefits of using industrial homogenizers extend far beyond achieving a uniform mixture. Consistent and reliable mixing contributes to multiple aspects of production efficiency and product performance. When particle size is controlled and ingredients are evenly distributed, it leads to enhanced product stability, reduced waste, and improved customer satisfaction. In highly regulated industries like pharmaceuticals and food, this consistency is crucial for compliance with safety and quality standards.
Additionally, the use of homogenizers can lead to cost savings by reducing the need for additives or repeated processing. Key advantages include:
- Improved texture and mouthfeel in food products
- Enhanced efficacy and bioavailability of pharmaceutical compounds
- Greater shelf-life and product stability
- Reduced energy and resource consumption due to efficient processing
By maintaining control over critical process parameters, manufacturers can fine-tune production to meet both regulatory requirements and consumer expectations. This reliability supports brand reputation and long-term operational success.
Choosing the Right Homogenizer for Your Needs
Selecting an appropriate industrial homogenizer depends on a variety of factors, including the nature of the materials being processed, the desired particle size, and production volume. Different homogenizer types—such as high-pressure homogenizers, ultrasonic homogenizers, and rotor-stator systems—offer unique advantages based on specific applications. Understanding the properties of your product and the demands of your production environment is key to making an informed decision.
Important considerations when choosing a homogenizer include:
- Viscosity and composition of the materials
- Required throughput and batch size
- Target particle size and distribution
- Sanitary and regulatory requirements
- Ease of maintenance and operation
Working with experienced equipment suppliers and conducting pilot tests can help ensure that the selected homogenizer meets both current and future production needs. Customizable configurations and modular designs also allow for scalability as business demands grow. Ultimately, investing in the right homogenizer contributes to process reliability, product quality, and operational efficiency.
Conclusion: Supporting Quality and Efficiency in Production
Industrial homogenizers play a vital role in ensuring consistent and reliable mixing across diverse manufacturing sectors. From food and beverages to pharmaceuticals and chemicals, their ability to deliver uniform particle size and stable mixtures supports both product performance and regulatory compliance. With features that enhance control, automation, and hygiene, these machines are well-suited to meet the demands of modern production environments. By carefully selecting and maintaining the right homogenizer, manufacturers can achieve greater efficiency, reduce waste, and deliver high-quality products that meet customer expectations.