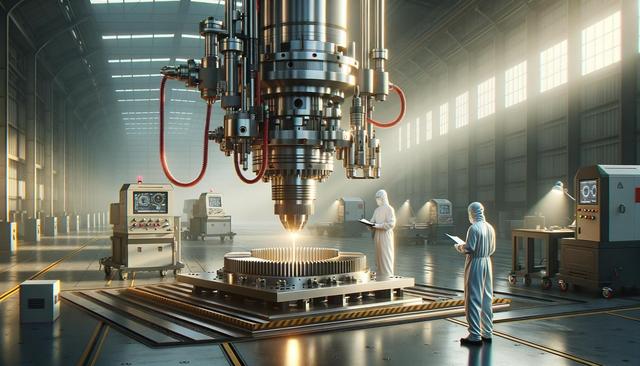
Precision and Power: Exploring Core Drilling Machines and Laser Cutting Technology
Understanding Core Drilling Machines
Core drilling machines play a key role in various sectors where material sampling and structural modifications are essential. These machines use rotating drills with diamond-tipped bits to extract cylindrical cores from solid materials. The core samples obtained are crucial for analyzing the internal composition, structure, and integrity of materials like concrete, stone, and asphalt. In construction, they are commonly used to test the strength and durability of building materials, while in geology they help in studying subsurface formations.
There are several types of core cutting machines, including:
- Handheld core drills for smaller, more accessible jobs
- Rig-mounted core drills for deeper and larger diameter samples
- Hydraulic and electric-powered models for different environments and material types
Safety and precision are paramount in core drilling operations. Operators must ensure proper alignment, cooling, and speed control to prevent equipment damage and achieve accurate results. The ability to create clean and uniform holes with minimal disruption to the surrounding structure makes these machines indispensable in critical infrastructure projects.
Applications Across Industries
The core cutting machine finds relevance far beyond construction and geology. In material testing laboratories, samples retrieved through core drilling help researchers and engineers assess the physical and chemical properties of materials. This data supports quality control, compliance with standards, and the development of new construction materials.
In road construction and maintenance, core drilling is used to examine asphalt layers and substructures. This information is crucial for:
- Determining the need for repairs or resurfacing
- Evaluating the lifespan of pavement
- Ensuring adherence to roadway construction standards
Moreover, industries such as mining and oil exploration rely on core drilling to understand mineral composition at various depths. This helps in resource estimation and planning efficient extraction methods. Each sector requires tailored equipment features, such as adjustable drilling speeds, different bit sizes, and varying levels of automation, to meet specific project demands.
Laser Cutting Technology: A Precision Tool
Laser cutting technology has revolutionized the way materials are shaped, modified, and processed. Using a high-powered laser beam, this technology enables precise cuts in metals, plastics, ceramics, and other materials with minimal waste and high accuracy. Unlike traditional mechanical cutting methods, laser cutting offers a contactless solution, reducing wear and tear on tools and allowing for intricate designs.
Key advantages of laser cutting include:
- Exceptional accuracy and repeatability
- Ability to cut complex shapes and fine details
- Minimal thermal distortion and material wastage
This makes laser cutting highly valuable in industries such as automotive, aerospace, electronics, and custom fabrication. Whether creating components for machinery or producing decorative patterns, the technology supports a wide range of applications with consistent quality and efficiency.
Comparing Core Cutting and Laser Cutting
Both core cutting and laser cutting technologies emphasize precision and power, but they serve distinct purposes and operate on different principles. Core drilling is primarily used for extracting material samples or creating circular holes in solid structures. It relies on physical contact and mechanical abrasion, which makes it suitable for deep penetrations and dense materials.
Laser cutting, on the other hand, is ideal for shaping and modifying materials without direct contact. It is most effective for sheet materials and offers unmatched precision for detailed work. The choice between the two depends on the specific requirements of a task:
- Use core drilling when material removal or cylindrical sampling is needed
- Choose laser cutting for intricate designs and high-speed production
While core cutting machines are essential for structural and analytical work, laser cutting excels in manufacturing and design. Understanding the strengths of each helps industries optimize their processes and improve project outcomes.
Future Trends and Technological Advancements
As technology evolves, both core cutting and laser cutting machines are becoming more advanced, efficient, and user-friendly. Automation and digital controls are being integrated to enhance accuracy, reduce human error, and increase productivity. For core cutting machines, innovations include improved cooling systems, noise reduction features, and smart monitoring for bit wear and performance.
In the realm of laser cutting, advancements are focusing on greater beam control, energy efficiency, and the ability to handle a broader range of materials. Developments in fiber laser technology, for instance, are enabling faster cutting speeds and lower operating costs. Additionally, integration with CAD/CAM software allows for seamless design-to-production workflows.
These improvements not only enhance the capabilities of the machines but also expand their applicability across new industries and use cases. As demand for precision and speed continues to rise, manufacturers and operators must stay updated with these technologies to maintain competitiveness and ensure high-quality results.
Conclusion: Choosing the Right Tool for the Task
Core drilling machines and laser cutting technology both play vital roles in modern industrial processes. For professionals in construction, geology, manufacturing, and testing, understanding the capabilities and limitations of each tool is critical. Core cutting machines offer the ability to extract material samples and make structural modifications with robustness and reliability. Meanwhile, laser cutting provides unmatched precision for shaping materials in design and production contexts.
Investing in the appropriate technology based on specific project needs can lead to improved efficiency, better outcomes, and reduced operational costs. As both fields continue to advance, staying informed about new features and best practices will be key to maximizing the potential of these powerful tools.