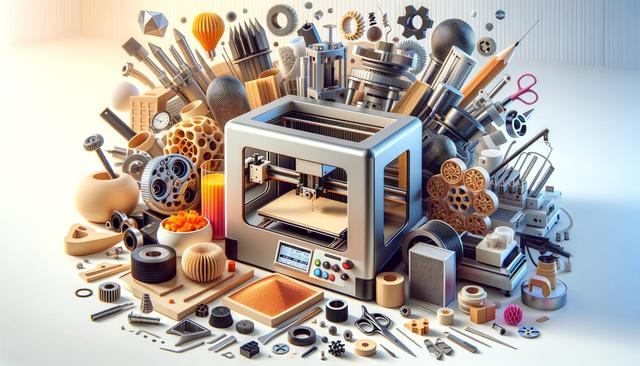
Rapid Prototyping and Machining Services: Compare Costs, Materials, and Lead Times
Understanding Rapid Prototyping and Machining
Rapid prototyping and machining services play a crucial role in product development, especially during the early stages of design. These services allow engineers and designers to quickly fabricate parts and prototypes using a range of techniques including CNC machining, 3D printing, and injection molding. Rapid prototyping focuses on speed and flexibility, enabling teams to test concepts, iterate on designs, and minimize time-to-market. On the other hand, machining services offer precision and durability, often used when a high-quality finish and tighter tolerances are required.
Choosing between these services depends on several factors such as the material requirements, complexity of the part, and the intended use of the prototype. While both options can produce functional parts, rapid prototyping is often preferred for initial design validation, whereas machining is utilized for end-use components or when tighter specifications are needed. Understanding the purpose of your prototype will help determine the most suitable approach.
Cost Comparison: Rapid Prototyping vs. Machining
Cost is one of the most significant considerations when selecting between rapid prototyping and machining services. Rapid prototyping, particularly 3D printing, often has lower initial setup costs, making it ideal for small-batch production and design iterations. In contrast, machining services may involve higher setup fees due to tooling and programming, but become more cost-effective at higher volumes.
Here are a few key cost factors to consider:
- Material usage: 3D printing typically uses just the amount needed for the part, reducing waste, while machining removes material from a larger block, potentially increasing material costs.
- Labor and setup: CNC machining requires more time for setup and programming, which can drive up labor costs.
- Part complexity: Complex geometries may be easier and cheaper to produce with additive manufacturing rather than subtractive methods.
In general, for one-off prototypes or low-volume runs, rapid prototyping is usually more economical. However, for precise, load-bearing parts or larger production runs, machining may offer better value over time.
Material Options and Their Impact on Selection
Material selection significantly influences which service to use. Rapid prototyping supports a wide range of thermoplastics and resins, suitable for visual models and functional testing. Common materials include PLA, ABS, PETG, and various photopolymers. These materials are generally suitable for parts that don’t require high strength or temperature resistance.
Machining services, on the other hand, offer a broader selection of engineering-grade materials, including metals such as aluminum, steel, titanium, and alloys. These materials provide superior mechanical properties, making them ideal for end-use parts and high-performance applications.
- Rapid Prototyping materials: PLA, ABS, TPU, nylon, resins
- Machining materials: Aluminum, stainless steel, brass, PEEK, Delrin
Choosing the right material depends on the prototype’s intended function. For example, if you’re testing a design for fit and form, a plastic prototype may suffice. But if the part needs to endure stress or heat, metal machining is likely the better choice.
Turnaround Times and Production Speed
One of the main advantages of rapid prototyping is speed. Depending on the size and complexity of the part, some 3D printed prototypes can be completed within a few hours. This fast turnaround allows for quick iteration, enabling designers to refine their concepts efficiently.
Machining, while generally slower due to setup and tooling requirements, can still offer fast lead times, especially for simple parts. However, as complexity and precision requirements increase, so does the time needed to complete the job.
Typical turnaround times:
- 3D Printing: A few hours to 2 days
- CNC Machining: 2 to 7 days, depending on part complexity and material
For urgent projects or early-stage validation, rapid prototyping provides the fastest route to a physical part. When quality and precision matter most, machining is worth the extra time investment.
Choosing the Right Service for Your Project
Deciding between rapid prototyping and machining services depends on the specific goals of your project. If you need a quick, cost-efficient model to test fit and design, rapid prototyping is often the right choice. It supports iterative development and enables teams to make swift changes before finalizing a design.
However, when the final part must meet strict specifications or be used in functional testing, machining services offer the accuracy and material options required. This is especially true in industries like aerospace, automotive, and medical devices where tolerances and mechanical strength are critical.
Key decision criteria include:
- Project stage: Concept validation vs. functional testing
- Material requirements: Plastic models vs. metal parts
- Budget: Lower initial costs vs. long-term production efficiency
- Time constraints: Speed vs. precision
Ultimately, many projects benefit from a combination of both services. Starting with rapid prototyping and transitioning to machining as designs mature allows teams to balance speed, cost, and quality effectively.
Conclusion: Making Informed Choices
For engineers, designers, and product developers, understanding the differences between rapid prototyping and machining services is essential to making smart, cost-effective decisions. Each method offers unique advantages depending on the stage of development, material needs, and performance expectations. By comparing costs, materials, and turnaround times, you can align your production strategy with your project goals. Leveraging the strengths of both approaches—rapid prototyping for speed and iteration, and machining for durability and precision—can lead to more successful outcomes and optimized workflows.