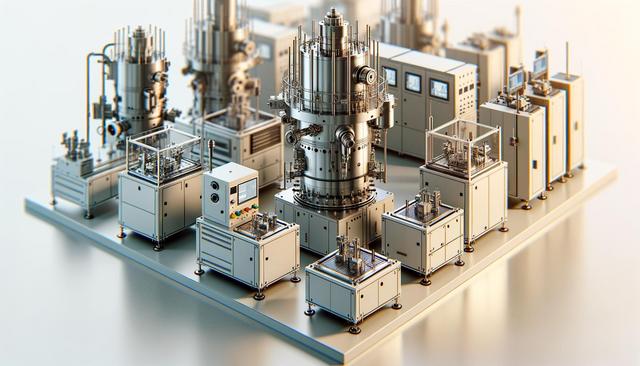
Semiconductor Processing Equipment: Solutions for Precision Manufacturing
Understanding the Role of Semiconductor Processing Equipment
Semiconductor processing equipment plays a central role in the production of microchips and integrated circuits, which power countless modern technologies. This equipment is engineered to operate under highly controlled conditions to support the delicate nature of semiconductor fabrication. The production process involves multiple stages, such as deposition, photolithography, etching, cleaning, and metrology, each requiring a distinct set of tools. These tools must not only perform with exceptional accuracy but also maintain consistency over large production batches. The complexity and scale of semiconductor manufacturing demand solutions that can deliver high throughput while preserving the integrity of microscopic features.
Precision is particularly important in processes like photolithography, where light is used to transfer patterns onto a wafer. Any deviation can compromise the entire chip’s functionality. Equipment manufacturers are therefore continuously innovating to improve alignment systems, optical components, and motion control technologies within these machines. The goal is to ensure that every layer of the chip aligns perfectly with the previous one, often at nanometer resolutions.
Key Attributes of High-Performance Equipment
To meet the rigorous demands of the semiconductor industry, processing equipment must embody several critical characteristics. These attributes help maintain the high standards required for device performance and yield. Among the most essential features are:
- Sub-micron level precision in patterning and etching
- High throughput to maximize production efficiency
- Contamination control to prevent defects
- Advanced automation for repeatability and process control
Modern equipment is often integrated with sophisticated software and sensors that provide real-time feedback and diagnostics. This allows operators to make adjustments quickly, reducing the risk of costly errors. Additionally, the use of predictive maintenance tools helps minimize downtime by identifying issues before they impact production.
Maintaining Cleanroom Standards
Cleanliness is non-negotiable in semiconductor manufacturing. Even the smallest particle of dust can render a chip defective. To address this, semiconductor processing equipment is designed to operate in cleanroom environments, often classified as ISO Class 1 to Class 5. This requires meticulous attention to airflow, material selection, and system sealing. Equipment must also be easy to clean and resistant to contamination.
Some of the strategies used to maintain cleanroom compatibility include:
- Hermetically sealed chambers to prevent particle ingress
- Use of ultra-clean materials and lubricants
- Laminar flow systems to direct clean air over critical components
These efforts ensure that particles, outgassing, and other forms of contamination are kept to a minimum, preserving the integrity of the wafers throughout the process.
Emerging Trends in Semiconductor Equipment Technology
As chip designs become smaller and more complex, the demands on processing equipment continue to evolve. New technologies such as extreme ultraviolet (EUV) lithography, atomic layer deposition (ALD), and advanced etching techniques are being adopted to meet these challenges. These innovations enable manufacturers to achieve finer feature sizes, greater performance, and lower power consumption in semiconductor devices.
Some key developments in the field include:
- Integration of machine learning for process optimization
- Modular equipment design for flexible manufacturing
- Improved energy efficiency and reduced environmental impact
The shift toward advanced packaging and 3D integration also requires new types of equipment capable of handling novel materials and process steps. As a result, equipment providers are expanding their capabilities and investing in research and development to stay ahead in an increasingly competitive market.
Challenges and Considerations in Equipment Selection
Selecting the right semiconductor processing equipment involves careful analysis of several factors. Manufacturers must consider not only the technical capabilities of the machinery but also its compatibility with existing processes and infrastructure. Cost, scalability, and service support are other critical considerations that influence purchasing decisions.
Key questions to address when evaluating equipment options include:
- Does the equipment support current and future node sizes?
- Is it adaptable to multiple wafer sizes?
- What is the expected maintenance schedule and cost?
- How well does the supplier support integration and training?
Making informed choices in equipment procurement can have lasting impacts on production efficiency, product quality, and overall competitiveness. As semiconductor devices become more integral to daily life, the pressure on manufacturers to deliver at scale and with precision will only grow.
Conclusion: Supporting Precision Manufacturing in a Dynamic Industry
Semiconductor processing equipment is foundational to the success of the microelectronics industry. As demand for smaller, faster, and more powerful devices increases, manufacturers must rely on equipment that delivers precision, reliability, and adaptability. Advancements in technology continue to push the boundaries of what this equipment can achieve, enabling new generations of semiconductors to reach the market. For those involved in semiconductor production, staying informed about equipment capabilities and industry trends is essential for maintaining a competitive edge and ensuring long-term operational success.