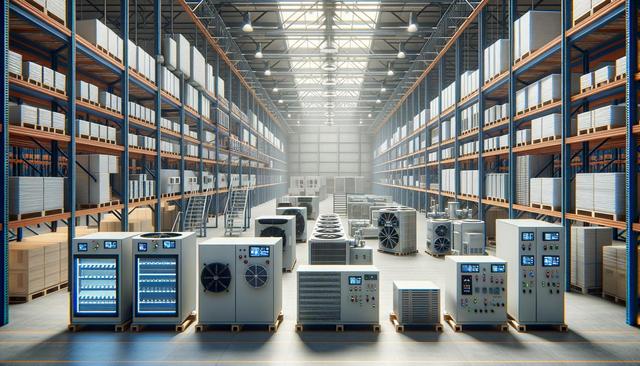
Warehouse Climate Management: Strategies for Regulating Temperature and Humidity
Why Climate Control Matters in Warehousing
Effective warehouse climate management is not just about comfort—it plays a critical role in maintaining the integrity and longevity of stored goods. Temperature and humidity fluctuations can damage a wide range of products such as food, pharmaceuticals, electronics, and even paper-based materials. For example, high humidity may lead to mold growth, corrosion, and packaging degradation, while extreme temperatures might compromise the chemical stability of certain products. Moreover, a well-controlled environment contributes to a safer and more productive workspace for employees. By regulating climate, warehouse operators can reduce spoilage, avoid costly losses, and ensure compliance with industry standards.
Key Factors Affecting Temperature and Humidity
Several internal and external factors can influence the climate within a warehouse. Understanding these elements is the first step toward effective climate management. Major contributors include:
- External weather conditions, such as seasonal temperature fluctuations and rainfall.
- Building insulation and structural integrity.
- Ventilation systems and airflow design.
- Heat generated by equipment and lighting.
- Moisture introduced through loading docks or uncovered areas.
Recognizing how these factors interact allows warehouse managers to tailor their climate control strategies accordingly. For example, warehouses in humid regions may require dehumidifiers, while those in colder climates might need additional heating solutions to prevent internal condensation.
Technologies for Monitoring and Control
Modern climate management systems offer precise control and real-time monitoring of warehouse conditions. These technologies help facilities maintain consistent temperature and humidity levels through automated adjustments and alerts. Common tools include:
- Thermostats and hygrometers for basic monitoring.
- IoT-enabled sensors that transmit data to centralized dashboards.
- Automated HVAC systems integrated with environmental controls.
- Energy-efficient climate control units with programmable settings.
Implementing such technology not only improves accuracy but also enhances operational efficiency. With real-time data, facility managers can respond to issues immediately, reducing downtime and minimizing risks to stored goods. Additionally, data trends can inform future infrastructure investments or policy changes within the facility.
Best Practices for Effective Climate Management
Establishing a proactive approach to climate control involves both technological solutions and operational protocols. Here are a few best practices to consider:
- Regular maintenance of HVAC and dehumidification systems.
- Routine calibration of sensors and monitoring devices.
- Sealing entry points to prevent air and moisture infiltration.
- Training staff to recognize signs of climate-related issues.
- Creating zoning strategies to isolate sensitive areas.
Incorporating these practices into daily operations helps maintain stable conditions and ensures long-term reliability. It also fosters a culture of accountability and responsiveness among warehouse personnel, which can contribute to improved quality control and inventory management.
Tailoring Climate Solutions to Specific Warehouse Needs
Not all warehouses are created equal, and climate control strategies should reflect the unique requirements of each facility. Factors such as the type of goods stored, building location, and operational hours all play a role in determining the ideal setup. For instance:
- Warehouses storing temperature-sensitive goods might benefit from zoned climate areas with independent controls.
- Facilities located in coastal areas may need enhanced dehumidification systems.
- Energy-conscious operations can explore solar-powered HVAC solutions.
Customizing solutions ensures that resources are allocated efficiently and that climate systems are neither overbuilt nor underpowered. A comprehensive site assessment, followed by collaboration with HVAC and environmental specialists, can lead to more effective and sustainable outcomes.